What is SELFOC®?
SELFOC® is a type of glass material with revolutionary functions. In a thin glass rod or filament, SELFOC® distributes light so that the refractive index decreases in a parabolic shape from the central to the peripheral areas. It is able to simultaneously transmit many types of light beams within a narrow space without disrupting the phases. Furthermore, when cut short, it becomes a highly functional lens with superior image transmission capabilities.
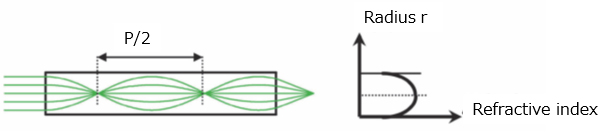
The refractive index is highest at the light axis (center line) and is distributed in a parabolic pattern to become increasingly lower at the periphery. For this reason, the internal light axis sinusoidally moves at a cycle pitch length P and repeats the image formation with each P/2 length.
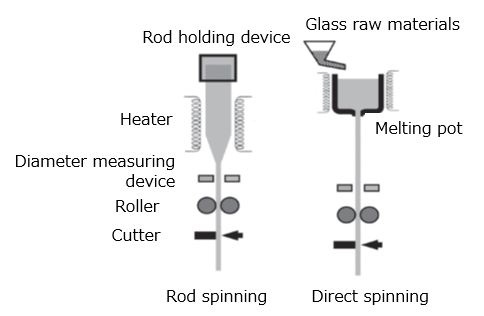
For rod spinning, rods of a few tens of millimeters in diameter are cut from a glass block and then heated and drawn. A continuous process that directly spins melted glass is also used.
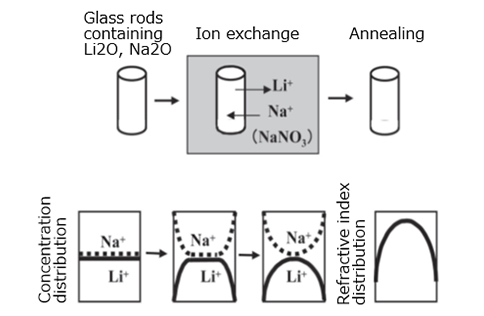
Rods containing the high refractive index component Li20 are submerged in a fused NaNO3 molten salt bath where ion exchange occurs.
The invention of innovative SELFOC® fiber
While light travels in a straight line at the shortest possible distance, research into ways to create and use bent light began in the 19th century. The 1960s saw the emergence of lasers, which spurred research into optical communication. But optical communication required long-distance transmission capability. At the time, while optical fibers were already being made industrially, the transmission distance was just a mere 10m because of the loss of light signals within the optical fiber with distance.
Against this backdrop, in 1965, the Company began research and development of glass optical fiber as an optical transmission line at the Amagasaki Research Center. In 1967, we began working with NEC Corporation, a company with top-level communication technologies, to conduct joint research on ways to transmit light within a glass fiber without deterioration.
It was known theoretically that transmission capacity could be increased if the light’s refractive index could be decreased in a parabolic shape from the central to the peripheral portions of the glass fiber. After countless experiments, the joint research team proposed an innovative method to vary the glass’s central and peripheral refractive indices by exchanging the ions within the glass with the ions outside the glass and announced this discovery in 1968. The invention of SELFOC® fiber drew attention around the world.
Challenges in working toward commercialization
・SELFOC® fiber
With the challenges of trying to suppress light signal loss and enhance fiber strength, a fierce competition in development ensued. After some 10 years of R&D, the Company was able to find solutions to these issues, and ahead of its competitors, succeeded in commercializing SELFOC® fiber, introducing it in 1978 under the product name of SELFOC®. In the same year, it was utilized as the world first for telephone lines commercially at Walt Disney World in the United States, with 200km of lines installed. This revolutionary piece of news won wide coverage in the media.
・Evolution as a microlens for optical communication
While SELFOC® was born in R&D of optical fibers, the Company was aware of its function as a microlens with a short focal length even in the early R&D stage. Hence, in parallel with R&D for its use as an optical fiber, we conducted R&D for its use as a microlens. Initially, optical fibers were multi-mode fibers, where transmission signals were easily disrupted, and hence, could not be used for long-distance communication. Long-distance communication required an optical fiber/photo semiconductor element coupler or optical divider between the optical fibers. SELFOC® microlens (SML®) was ideal for these applications, and vast amount of SML®s were adopted in optical communication. In the 1980s, Bell Laboratories decided to use SML® for the optical source modules in its trans-Atlantic cables, giving the Company a huge order to deliver.
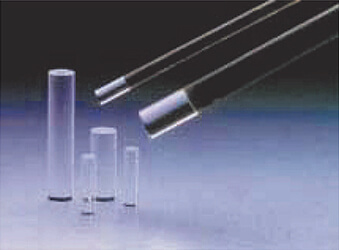
The refractive index varies inside the glass. As a result, both flat ends of the rod act as a convex lens.
SELFOC® microlens (SML®) applications
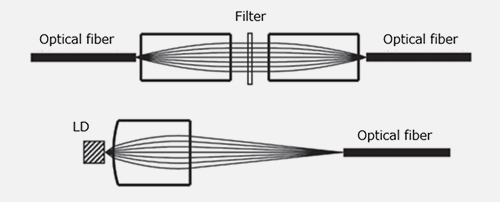
- (Above) An example of two optical fibers combined through a filter
- (Below) An example of an outgoing light beam from an LD (laser diode) sent to an optical fiber
Development of SELFOC® lens array (SLA)
Development of SLA was being conducted in parallel with SML®. One of the characteristics of SELFOC® is its ability to create an erect and equal size image with by choosing the appropriate lens length. Utilizing this characteristic, the Company developed SELFOC® lens array (SLA), which was composed of hundreds of thousands of SML® arrayed in one or more lines to create one linear image. SLA had superior resolution and could create a uniform, erect and equal magnification image at the contact position to an object. At the time, copiers used conventional lenses that required complex optical systems and a distance of 60cm or more between the paper and the image plane. In 1978, the Company created a revolution in the copier business with its introduction of the first SLA6 (aperture angle: 6 degrees), where the distance between the paper and image plane was reduced to a mere few centimeters. This SLA was employed by such companies as Ricoh Company Limited and Minolta Co., Ltd.
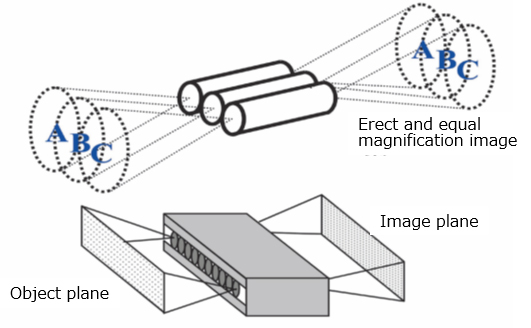
Lining up small, upright, equal magnification lenses side by side creates a compact and optical linear image.
Evolution and expansion of SLA lineup
In 1980, the Company established a plant in Sagamihara, Kanagawa Prefecture, introduced SLA9 with a 9-degree aperture angle in 1982, and SLA20 with a 20-degree aperture angle in 1984. The SLA20, with its wider aperture angle resulting in the brighter image despite the shallower depth of focus and larger chromatic aberration, was broadly adopted in facsimile machines, which were rapidly gaining popularity at the time. In addition, the Company developed SLA12 for copiers, whose market was experiencing rapid expansion and becoming more highly advanced. The SLA12 won recognition for its high resolution and very small chromatic aberration.
Since then, SLAs have become increasingly smaller and the diameter of each lens fibers, which initially had been slightly larger than 1mm, became 0.9mm, 0.6mm and 0.3mm, enabling a greater number of applications.
Rapid growth of SLA
Demand for lens arrays rose with the gradual decline in analog copiers and the growing popularity of image scanners to replace them. Lens fiber diameter of SLA could be produced as small as 0.3mm, and the SLA12E, which reduced the distance from the image plane to the object to 10mm or less, was used for contact image censors (CIS) and increased market share by steadily replacing complicated optical reduction system . With the emergence of multi-function printers (MFP), which combined inkjet printers with image scanners, demand for SLA12E, which was adopted in MFP, exploded in 2003 and beyond. At the same time, the Company began selling linear LED light source products of SELGUIDE(SG)too, which was used in combination with SLA12E. NSG’s SLA became an indispensable component of MFP, and the Company acquired the dominant market share.
To respond to this increased demand for SLA, the Company significantly increased the production capacity at its Sagamihara plant and Suzhou NSG Electronics plant in 2004. Since then, SLA demand for MFP has continued to grow, which has been met with additional increases in production.
The challenges in lead-free SLA development
Lead has long been used in glass to achieve high refractive index and facilitate melting and molding processes. The glass for SLA, except for certain models, also contained a small mole percentage of lead. However, with a lead-free movement gaining ground globally, the Company started work to develop a glass composition that eliminated lead from the glass for SLA around 1999. The development went through difficulties since removing lead from glass usually resulted in higher probability of devitrification and lower stability in production. However, after many R&D works with trials and errors, the Company finally succeeded in removing lead from all types of SLA products in 2009.
Moving forward with further advances
Coinciding with NSG’s 100th anniversary in 2018 is the 50th anniversary of the SELFOC® announcement in 1968. SELFOC® has grown with optical communication and paper culture, but it is sure to grow further and open new markets in the future.