Background of APBL development
Automotive windshields are made of laminated glass to reduce the damage it may inflict on the driver and passengers and to prevent scattering, even when broken.
Automotive windshields are manufactured either using the “sag bending process” where the glass is allowed to sag under its own weight onto a mould placed under it, or the “press bending process”. The press bending process enables more complex shape than sag bending, making the production of products with high surface accuracy possible.
NSG and Pilkington manufactured laminated glass by separately pressing two sheets of glass and then laminating them. But to further improve the technology, in the 1990s, Flachglas (currently Pilkington Automotive Deutschland) developed its own new glass pressing process called APBL (Advanced Press Bend for Lamination). In 2005, the Company obtained the first APBL from Pilkington Deutschland and installed it at the Maizuru Plant and since then, has responded to automobile manufacturers’ increasing demands for higher quality products through ongoing improvements and at the same time, enhanced processes to improve flow rate.
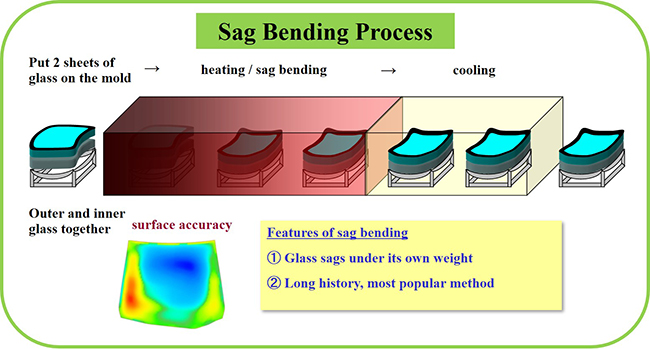
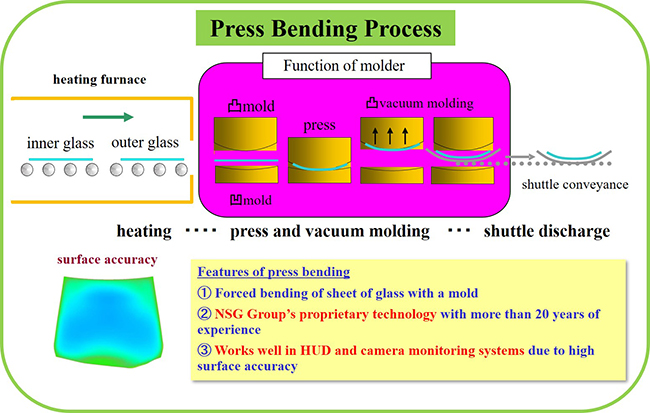
APBL as the synthesis of NSG Group’s comprehensive technical capabilities
Starting in the 1990s, the demand for thin, large-sized and high surface accuracy automobile windshields increased with a diverse range of new automobile designs and the need for greater fuel efficiency. In the 1980s, the U.S. firm Libbey Owens Ford (LOF, currently Pilkington North America) developed CPBL (Conventional Press Bend for Lamination), a press bending technology for windshield where individual sheets of glass are pressed and then laminated together to produce windshields. LOF became a part of the Pilkington Group in 1986 but NSG had a long active technology exchange program with LOF prior to 1986. In addition, NSG signed an R&D collaborative agreement with Pilkington in 1988. In 1990, NSG obtained CPBL equipment from Pilkington North America and installed it in Kyoto Plant.
With CPBL, NSG was able to manufacture and supply windshield for Toyota’s high-end luxury cars and others. But by 1995, the Company developed its own unique method called eCPBL, which used the vacuum process to further enhance surface accuracy. This technology was used at the Witten Plant of Pilkington Automotive Deutschland and process was finished with APBL.
With eCPBL, the glass was transported from the furnace on rollers and then shaped in a vacuum process using presses. However, some of the final products showed deformations because of the rollers. Since this could distort the view of the driver, technology to minimize this distortion was needed, in particular for large-sized, complex shape windshields. In addition, glass that did not conform to standards was rejected during inspection, affecting production yield and delivery dates. To resolve these fundamental problems, the Company developed a new glass transportation method to float on air instead of rollers. This revolutionary transport method was born from an idea that went through numerous stages of trial and error before becoming finalized.
In this manner, APBL was the synthesis of the technical expertise of NSG, LOF and Pilkington working together in a technological collaboration.
Challenges at the Maizuru Plant
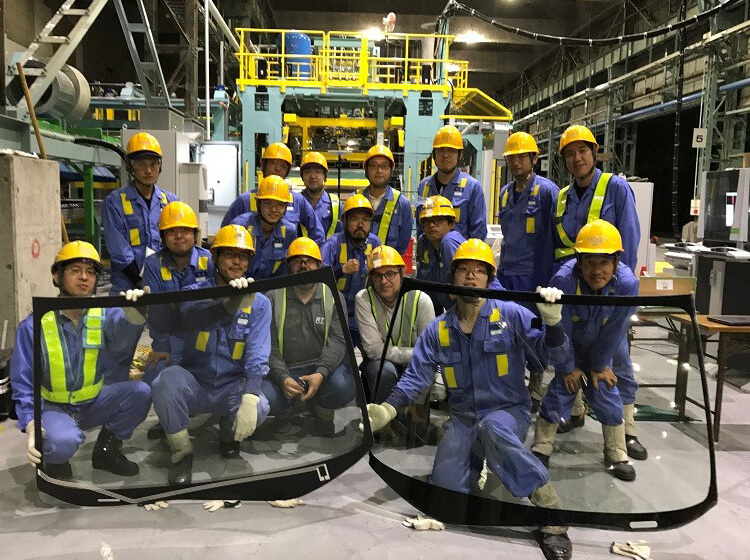
at the Maizuru Plant #2 Furnace
Challenges at the Maizuru Plant
In the 2000s, automobile manufacturers began to require large-sized, high-surface-accuracy windshields. The Maizuru Plant decided to install the first APBL designed to manufacture large-sized windshield from the Pilkington Automotive Deutschland Witten Plant. The construction work at Maizuru Plant was completed in 2005. With this, it became possible to produce a windshield that was 2000mm x 1400mm in size, larger than the conventional windshield manufacturing method which has a maximum size of 1800mm x 1100mm. Furthermore, efficiency would be vastly improved because the cutting process to final inspection stages on the production line are directly connected. However, after installation of the new equipment, the process did not work initially as expected. The Company declared a state of emergency, during which they worked through the weekends for six months, and asked customers for their understanding for schedule inconveniences. Finally, all problems were resolved.
New demand for the world’s largest HUD
More and more cars are introducing head-up displays (HUD), which project information on to the windshield. However, if the glass shape diverges from the design shape, the image projected may not match the actual shape of the road. The Maizuru Plant used a number of different types of simulation technologies and fine-tuned each manufacturing process and criteria, including the mould surface shape. With this effort, the Company was able to successfully produce a maximum 25-inch wide HUD. This is currently the largest HUD in the world. With the growing popularity of advanced driver-assistance systems (ADAS), the demand for high-surface-accuracy windshield is expected to rise even further in future.
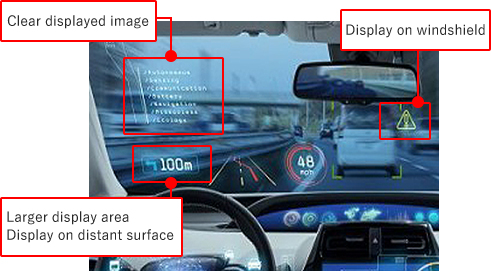
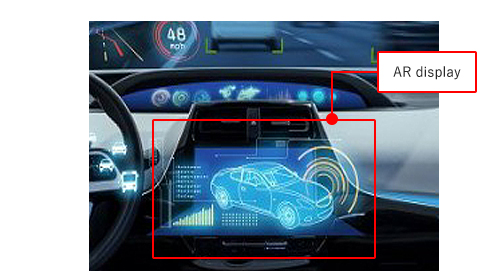
Global expansion
One year after APBL was implemented at the Maizuru Plant in 2005, the Pilkington Group became a part of the NSG Group. APBL, which initially was developed at the Witten Plant of Pilkington Automotive Deutschland, was fine-tuned to respond to market demand, and was installed at the Maizuru Plant as its second line in 2017. With advances in automobiles, the need for high-performance windshields increased globally. Therefore the NSG Group installed APBL for the first time in the Poland Plant in 2013 and the Versailles, Kentucky (U.S.A.) plant in 2015. In addition, it added a second line in Versailles and a new line in San Salvo, Italy, in 2017, thus creating global infrastructure to supply all major markets.
With demand expected to increase even further, the NSG Group will continue its evolution as technological leader.