Breakthrough in automotive glazing
In the 1970s, automotive glass was manufactured using the tong-holding method, which resulted in tong marks on the finished product. When the oil crisis hit Japan around 1975, demand for energy-efficient vehicles also created a need for lighter, more aerodynamic glass. To overcome problems associated with the tong-holding method and to meet the demand for high-performance automotive glass, NSG developed a “horizontal tempering method” that poured glass horizontally and press molded and reinforced the glass in a single stage. This method, based on the company’s proprietary technology, was named Nippon Sheet Glass Horizontal Press (NHP) and was installed at the Maizuru Plant in 1985.
Conventionally, glass was pressed and then quenched to temper it in a 2-stage process. Since the glass would cool during the extended process, there was a limit to how thin it could be made. With the new process, however, glass would be pressed and quenched in a single stage, allowing for the production of thinner sheet glass.
Through later collaboration with Pilkington, NSG developed additional processes such as pre-bending technology before the press stage, which enabled manufacture of deep bent glass, and vacuum process technology which provided capability to meet demand for a diverse range of curved glass.
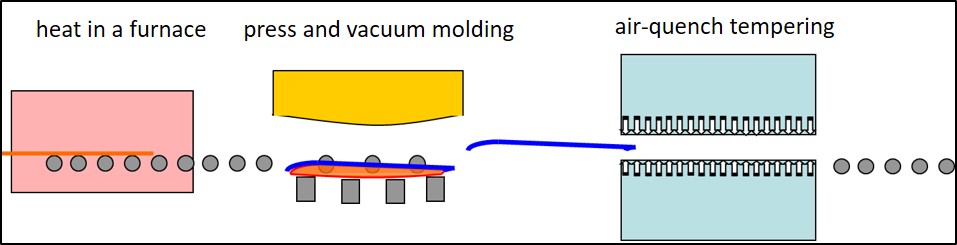
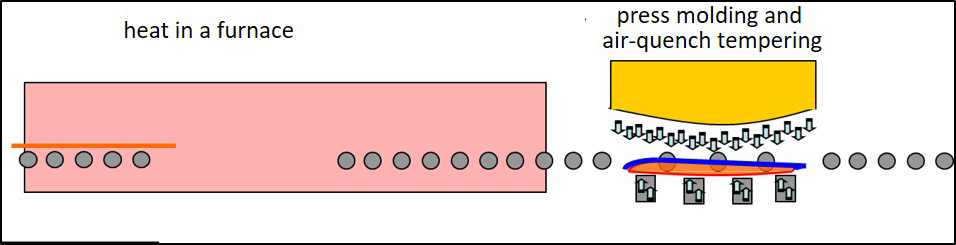
Challenges in NHP development and installation of the Maizuru Plant’s number 1 furnace
In the late 1970s, the Company concluded that the only way to resolve issues resulting from the tong-holding method was to transfer glass horizontally. The basic concepts with in-house development of this technology were finalized in July 1981. In July 1982, NHP-D (development) was installed for experimental development purposes at the Kawasaki Plant.
After two years of repeated experiments and process improvements, the Kawasaki Plant was finally able to produce intended results using the horizontal process. In October 1984, the Company decided to formally install NHP and in August 1985, completed construction of the NHP-1 Horizontal One-Stage Process furnace.
Because NHP strengthens glass while press bending, it proved to be a highly efficient manufacturing method that helped improve the quality and provision of NSG products. While the line was developed specifically for shallow-shape bending, it was later remodeled for deep-shape bending as well. By combining press bending and vacuuming, the Company was able to produce a diverse range of curved glass with improved surface accuracy, to meet the demands of a rapidly changing market.
Investing in state-of-the-art technologies for the future and achieving the world’s thinnest glass
Unsatisfied with their success and anticipating a need for small-radius bends, the Company decided to embark on the development of a specialized furnace. In June 1987, NHP-2 was put into operation, enabling deep, small-radius and three-dimensional bending with NHP. This unique production technology was something that competitors did not have. The Company also continued its pursuit of producing thin glass that retained strength and succeeded in reducing the thickness from 3.5mm to 3.1mm and, then later in a world first, further to 2.3mm in thickness. This helped contribute significantly to making glass lightweight.
NHP-1 and NHP-2 continued to operate smoothly, and thanks to NHP, NSG products were regarded highly and demand continued to grow. In March 1990, the Company reevaluated the plant layout and constructed the NHP-3 line with the same capacity as NHP-2 but at half the length. With this, the Company was able to increase manufacturing capacity and lower costs.
Development of the Prius Double-Bubble Backlight and commendation
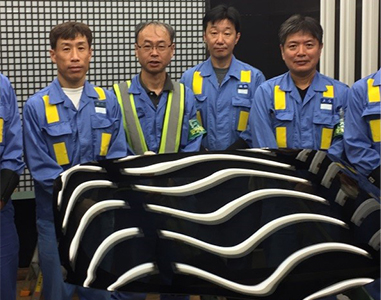
Because of the ability to produce complex and high-performance glass with NHP, Toyota Motor Corporation asked NSG to produce double-bubble rear windows for its new Prius model. To confirm the technological feasibility in-house, upon the proposal of NSG Japanese engineers, Italian R&D coordinators arranged to have experiments conducted at the German plant. The outcome of the trials confirmed that production could be managed with the Company’s equipment. This success was a collaborative effort of the Group’s Japanese, Italian and German engineers.
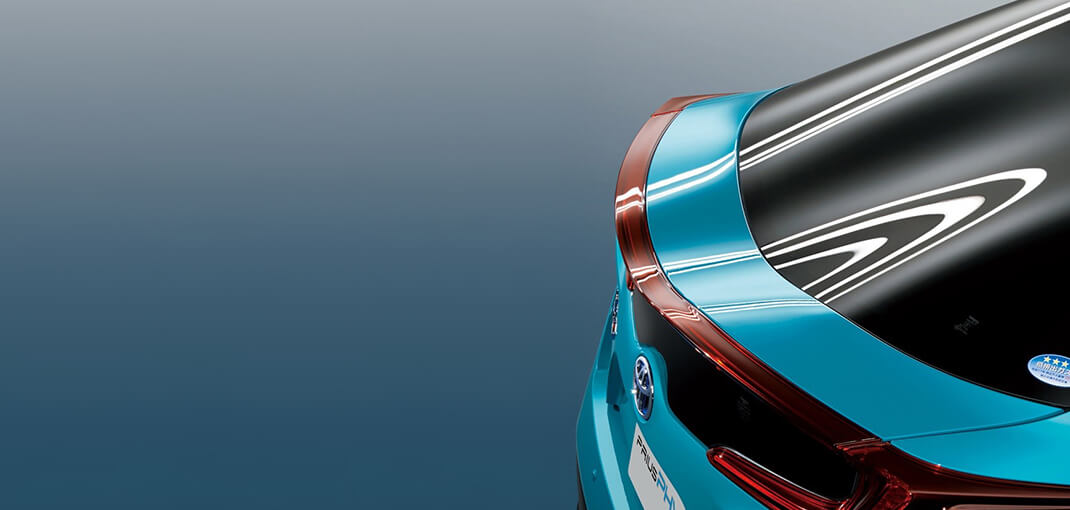
The Prius PHV, which features NSG’s double-bubble back light, won Car of the Year Special Prize in the Innovation Category.
With this achievement, the Company received an order to participate in the design proposal and manufacture of a complex-shaped rear window. Following this achievement, NSG engineers developed an in-house system that manages the bending and reinforcing of glass by computer. After repeated simulations and fine tuning with Toyota engineers, the design of a double-bubble backlight was finalized. To manufacture this product, it was decided to use the suction process, which makes the shape perfectly match the recesses and, in 2016, mass production began.