What is Spacia™ vacuum glazing?
Almost the same thickness as a single pane with four times the insulation
Spacia™ is the world’s first commercially viable advanced vacuum insulated glazing, launched in October 1997 by Nippon Sheet Glass (NSG). It uses special metal film coating technology and a vacuum process to create a 0.2 mm wide vacuum space between two panes of glass. This results in a thin, yet highly insulating vacuum glazing that overturns conventional wisdom about double glazing. Despite being only around 6.2 mm thick, Spacia™ insulates roughly twice as much as regular 12 mm double glazing, and about four times as much as a single pane of glass. This not only helps maintain a comfortable room temperature, but also saves energy and prevents condensation.
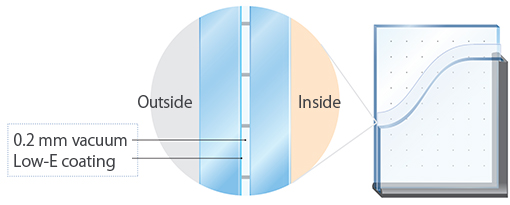
The invention of vacuum glazing technology and its introduction to NSG Group
The idea behind vacuum glazing is not new. It was first described in 1913 and patented in the United States in 1921. But designing something that could withstand the pressure of the vacuum and that was suitable for mass production proved difficult, and it remained an unachievable technology.
In 1987, with interest in energy-saving technologies after the first oil crisis, Professor Richard Collins at the University of Sydney began actively researching vacuum glazing and its insulation-boosting effects. In 1989, Professor Collins and his student Stephen Robinson successfully test-manufactured several experimental samples, demonstrating that laboratory production was achievable and that mass production may be possible. Over the period of 1989 to 1993, Professor Collins gave presentations on this technology to many major glassmakers and window glazing companies around the world. No one, however, expressed serious interest.
Crucial Encounter
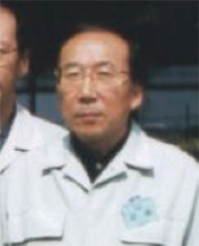
Head of Development
In 1993, Professor Collins met an distinguished doctor of an industrial institute in Japan and expressed his wish to develop a commercial relationship with a manufacturer for vacuum glazing. In response, the doctor contacted the President of Nippon Sheet Glass at the time, who then asked Hideo Kawahara, Head of Development of Constructural Glazing to consider this project. Mr. Kawahara went immediately to meet with Professor Collins, who was in Japan at the time, and requested samples.
At the time, the conventional way of dealing with the cold weather in northern parts of Japan was to install regular double glazing which required wide window frames. If vacuum glazing could be mass produced, then a business opportunity to replace the glass in the existing frames might emerge.
Although Professor Collins had discussions with several other glass companies around the world, Mr. Kawahara was the only person who expressed a serious interest in the technology. Their encounter was to have significant impact on NSG years later.
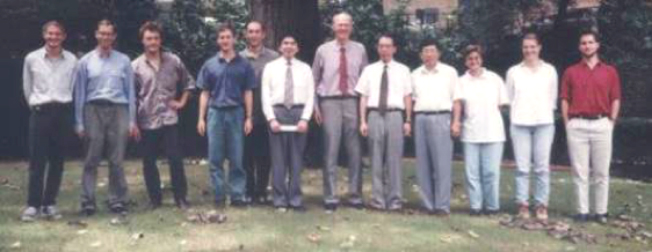
Joint Project Team of Manufacturing, Sales and Development
In 1994, NSG entered into a formal licensing and collaborative research agreement with the University of Sydney. Following the technology transfer preparation at NSG’s Itami Research Institute, a pilot production facility was opened in the Kyoto Plant to begin collaboration with Professor Collins’ team to improve product performance and explore mass production methods. Although NSG adopted the basic idea from the University of Sydney, applying it to mass production was a difficult task. A project team was formed in 1996, but since the target market for vacuum glazing would be ordinary households, the team worked on everything from development and manufacturing to marketing. Until then, NSG had been focused on producing float glass for the wholesalers, so this was the first time it had set up a project team which included marketing of the finished product. The slogan of the project team was “promote the integrated effort of technology, manufacturing and marketing.”
Technical Challenges for Industrialization
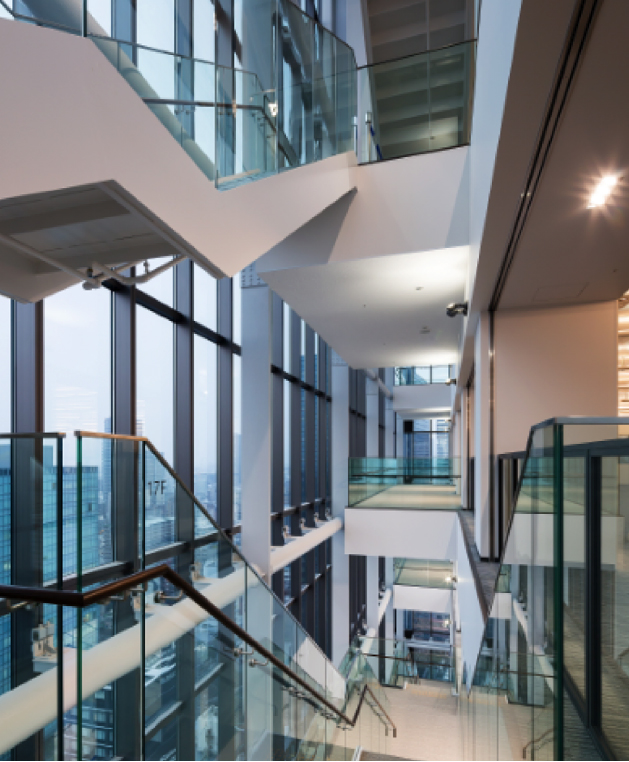
Technical Challenges for Industrialization
When this project started, Dr. Collins’s research was just at the stage of investigational basic technology in the laboratory. Numerous technical hurdles still had to be cleared to adopt the experimental vacuum glazing technology for mass production. For many years, the teams at NSG and the University of Sydney worked in close collaboration to address these challenges. The two teams worked on their specialized areas of expertise and shared technical issues and concerns as they arose. In several cases, it was necessary to repeat earlier work, and entirely new technological approaches had to be developed. Despite numerous unexpected setbacks and substantial cost, NSG never wavered from its commitment to achieve success from this technology.
One early challenge was how to efficiently arrange the microspacers to maintain vacuum space between the two glass sheets under high atmospheric pressure. How to produce these vacuum glazing products in large quantities was another big issue.
Microspacer Placement Technology
Vacuum glazing involves creating a vacuum layer between two panes of glass but the atmospheric pressure of ten tons per square meter means the microspacers have to be placed in such a way to keep glass panes separated. However, the number of microspacers must be kept as few as possible because they conduct heat. Technical experts at Nippon Sheet Glass Engineering tackled this problem. Since there was no equipment that could efficiently place the microspacers, it took two years and numerous trials and errors for the engineers to design and develop a machine for arranging and placing the microspacers. This was an outstanding breakthrough and the same basic technology is in use to this day.
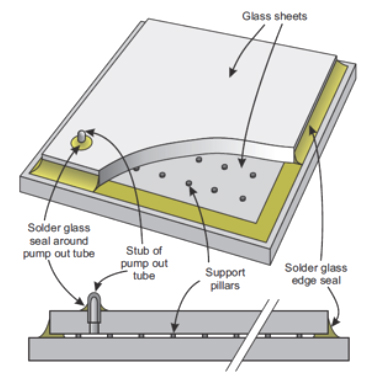
Mass Production Challenge
At that time, vacuum pumping technology was for manufacturing cathode ray tubes (CRT) with a separate vacuum pump for each CRT, which was not efficient. Though several companies were asked if they could develop a method to mass-produce vacuum glass, only one contractor responded. While the design work progressed on the assumption that mass production of vacuum glass was possible in theory, the contractor would not guarantee whether the machine would actually work. In the end, the machine did achieve the expected level of performance, and the issues of placing microspacers and mass-producing vacuum glass were resolved.
In January 1997, successful development of Spacia™ vacuum glazing was announced and the product received the “Excellence Award” of the Nikkei Superior Products and Services Award in the same year.
Marketing Initiative and Award Winning
As this was NSG’s first product for consumers, the project included the marketing plans right from the start. Among the over 500 candidates for a brand name submitted by the employees, “Spacia™” was selected. In January 1997, after announcing the successful development, test marketing was conducted with employees and also in limited regions to identify potential issues for glass distributors in terms of marketing and fitting methods. Distributors were trained accordingly and the full-scale sales launch started in October that year. By that time, the company had set up its first call center and a network of 1,000 Spacia™ distributors in Japan.

Expanding Sales and Production
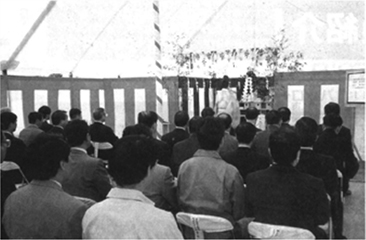
Expanding Sales and Production
In winter of 1997, shipments could not keep up with the incoming orders. Although the market for home renovation was the main target of marketing, it became clear that homeowners did not order glass from the retailers. In response, NSG placed newspaper ads to increase awareness of the Spacia™ brand and asked the retailers to distribute leaflets in their neighborhoods. In addition to ramping up production capacity at the Kyoto plant, the new plant was opened in Ryugasaki, Ibaraki Prefecture in April 1998. Other improvements in production and quality control included the development of an automatic calculation system to ensure efficient production of products in various sizes with short delivery deadlines.
Expanding the Spacia™ Lineup and Award Winning
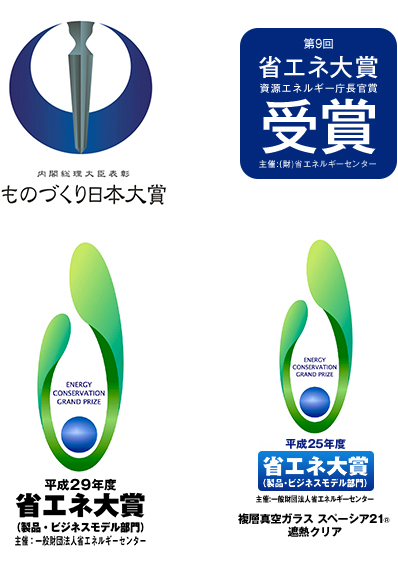
Expanding the Spacia™ Lineup and Award Winning
NSG continued expanding the Spacia™ vacuum glazing lineup by combining various features with its insulation performance with a series of launches, including “Spacia21™” double glazing vacuum glass in 2002, the laminated Spacia Shizuka™ in 2004, Spacia™ Cool vacuum glazing in 2012, “Spacia21™” clear thermal shield unit in 2013 and the advanced vacuum insulating glass “Super Spacia™” in 2017.
Spacia™ products have won the Energy Conservation Grand Prize three times (Spacia™ in 1999, Spacia21™ clear thermal shield unit in 2013 and Super Spacia™ in 2017). In addition, Spacia™ vacuum glazing won the 2007 Monozukuri Nippon Grand Award from the Ministry of Economy, Trade and Industry for its acclaimed technology.
Continued Development of Spacia™
With the launch of TV commercials in 2011, the product gained further recognition among consumers. Appreciated for its efficiency, Spacia™ was used not just in private homes and apartments, but also in commercial spaces such as convenience stores and restaurants with large glass facades and long business hours. It is increasingly used in food display cases and industrial refrigerators, where visibility as well as strict temperature control are required. NSG continuously strives to develop and expand Spacia™ to meet a variety of uses, taking full advantage of its unique features to grow with changing lifestyle.
Message from Richard Collins Emeritus Professor, The University of Sydney 2018
My vacuum glazing journey began in 1987 with a "crazy idea" – or so many thought! Two years later, my student Stephen Robinson made the world's first thermally insulating vacuum glazing sample. Over the next four years, my group's understanding of this technology rapidly expanded. Despite sustained efforts, however, I was unable to establish a collaboration to develop vacuum glazing commercially. In 1993, Hideo Kawahara and NSG accepted this challenge. I am immensely proud of what our collaborating teams subsequently achieved. I am also grateful that, despite many daunting technical and commercial issues, NSG's commitment to the development remained unshakable. I am privileged to be part of the success of Spacia™.
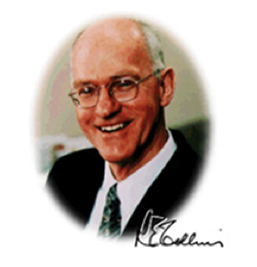
University of Sydney