Invention of the Float Process
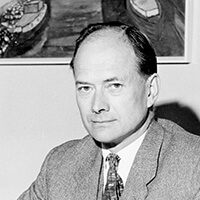
Pilkington
While the Colburn and Foulcault processes invented in the early 20th century ushered an era of mass production of sheet glass, neither method could easily produce a perfectly flat plate of glass of uniform thickness. For that reason, polished plate glass was used for high-quality applications, such as mirrors and automotive glass.
With time, a method that combined the beauty of plate glass made with furnaces and the evenness of polished plate glass was developed by Sir Alastair Pilkington who was in charge of technology at Pilkington Brothers of the United Kingdom. In 1959, this method was introduced to the world as the float process.
The float process is an innovative method where molten glass is poured onto a bed of molten tin metal in a float bath to create a perfectly flat sheet of glass with uniform thickness, thanks to weight and surface tension characteristics.

Sir Alastair graduated from Cambridge University in 1947 and joined Pilkington to work on the difficult challenge of making distortion-free flat glass using a conventional furnace. While the idea of making perfectly flat glass using surface tension was considered in the past, determining what substance to use to support the glass was the problem. While helping in washing dishes after dinner one day, Alastair saw how the oil floated on the surface and thought “what if glass is floated on liquid?” It was 1952.
Although Sir Alastair understood the principle, translating it into a practical application was no easy matter. He began experimenting in December that year and though imperfect, he made a flat piece of glass. In 1954, after countless experimental productions, he was able to make a 76 cm width machine with near-satisfactory results. In 1955, Pilkington formally decided to build float process machines and after seven years of effort and 4 billion yen in R&D expenses, a sheet of glass made entirely by the float process was produced in July 1958.
Introduction of the Float Process
The float process was highly regarded worldwide and every major sheet glass manufacturer tried to implement the technology. In January 1959, just one week after the announcement of the float process, NSG contacted Pilkington about licensing of this technology. Two years later in the fall of 1961, Fumio Nakamura, NSG president, visited Pilkington to express a desire to implement their technology. In July 1963, Itsuro Watanabe, Nakamura’s successor, reached a general agreement regarding technology licensing during his trip to the U.K. In March 1964 in London, the two parties signed a technical licensing agreement on the float process.
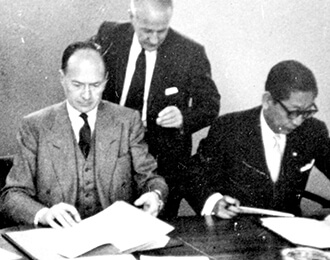
Construction of Float Lines
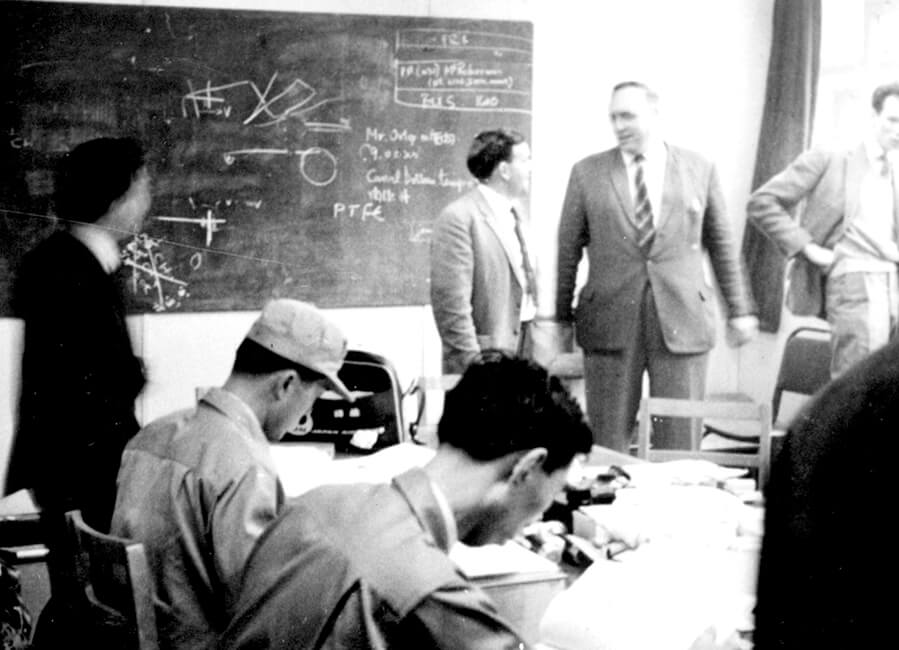
Construction of Float Lines
In August 1964, Managing Director Mitsuki Miyazaka led a group of engineers and designers to visit Pilkington and study the technology. Compared with other Western companies that had already licensed the technology, NSG had a shorter construction time frame and a more detailed analysis which surprised Pilkington.
When the engineering team returned to Japan, the decision was made to convert the No. 3 furnace of Maizuru Plant into a float furnace by November 15, 1965.
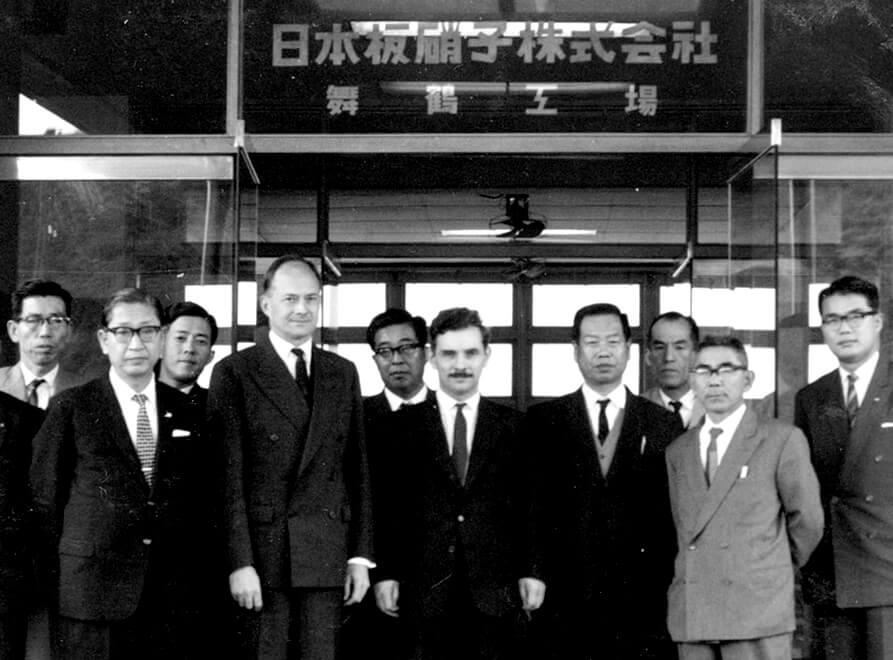
(from the front left, Managing Director Takimoto and Sir Alastair Pilkington)
In the course of construction, Pilkington dispatched its engineers to start the installation work in July 1965. In September, 15 NSG engineers were sent to Pilkington to study the float process and on-site operations. Features that had not been considered in the U.K., such as anti-earthquake measures, were newly incorporated in the design.
To produce glass at fast speeds using the float process, a continuous direction conversion device and branching device were installed for the stages after the plate glass was cut. To avoid scratches on the glass surface, newly developed air tables were installed.
A group photo at the Maizuru Plant
(from the front left, Managing Director Takimoto and Sir Alastair Pilkington)
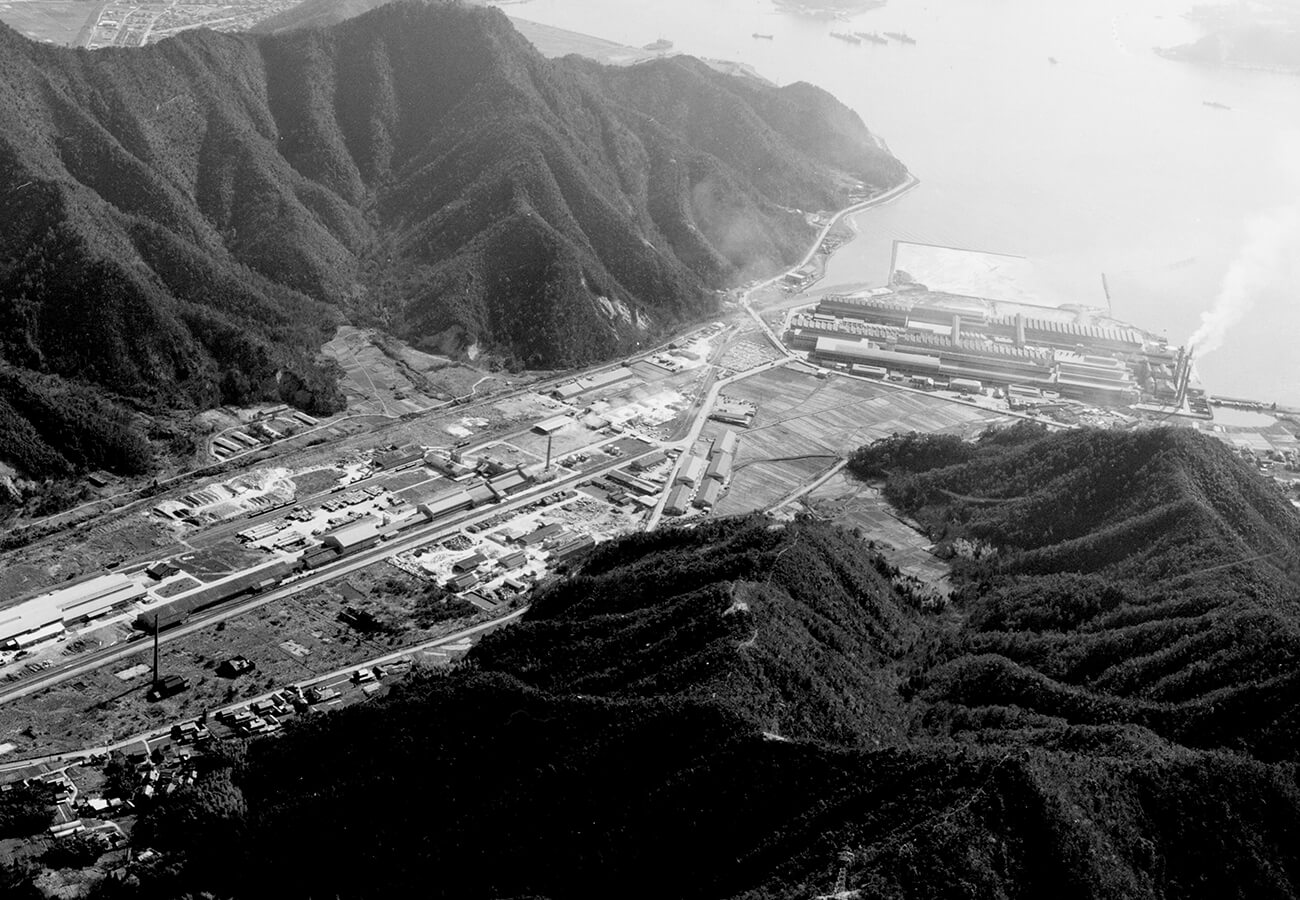
Construction of the float line progressed on schedule and in October 1965, the melting tank was lit. Overcoming language barriers and other issues, the float line began operations on November 15, 1965.
On that day under the steadily falling snow, Maizuru Plant was filled with an air of excitement. At 10:30 AM, while Chairman Nakamura and other senior managers held their breaths, President Watanabe opened the valve for the molten glass to flow into the float bath. Soon, a sheet of glass passed through a long slow cooling kiln and about 40 minutes later, emerged from the front. This is how the first float glass in Asia was produced.
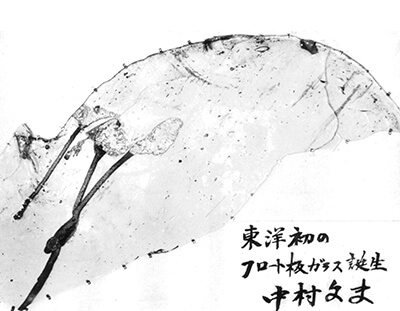